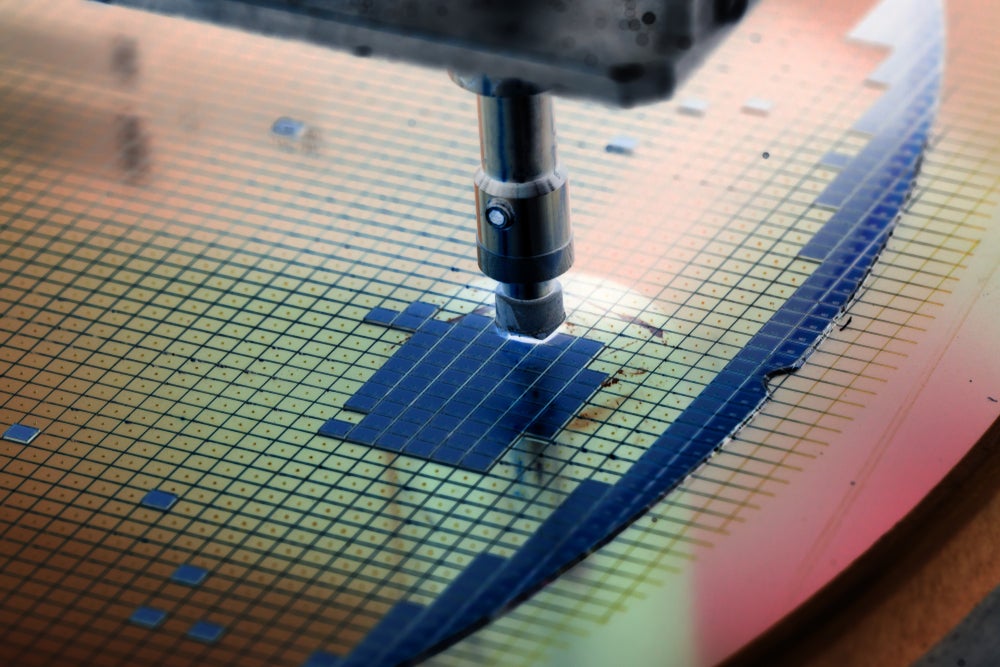
Impact of the Chip Shortage on the Vehicle Sector
An almost two-year-long semiconductor shortage is expected to ease in the second half of 2022, but rising costs in battery construction for global auto manufacturers offer fresh grounds for concern, according to automotive experts.
Global auto manufacturers have experienced a tumultuous last two years characterised by Covid-19 lockdowns, assembly plant closures, falling demand for new vehicles and significant delays in the microchip supply chain.
But, as governments unwind their pandemic restrictions this year, the auto sector is expected to experience “substantial pent-up demand which manufacturers cannot meet,” according to Paul Lund, head of industrial ratings for Europe, the Middle East and Africa at Fitch Ratings.
Lund said that while bottlenecks in semiconductor availability will ease this year, he warned that rising prices for raw materials, particularly metals, threaten to upset automakers’ plans to transition from internal combustion engines to electric vehicles.
Calum MacRae, head of automotive R&A at GlobalData, struck a less optimistic tone: “We’re not out of the woods yet regarding the chip crunch. Already this year we’ve seen Toyota’s operations cut because of the chip shortage in facilities in Japan and North America, while at the weekend Ford announced disruption to its build plans in North America for the month. However, we expect these issues to subside as we move through the year with the peak of the chip crisis passing in Q3 2021.”
Auto finance
How well do you really know your competitors?
Access the most comprehensive Company Profiles on the market, powered by GlobalData. Save hours of research. Gain competitive edge.
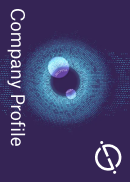
Thank you!
Your download email will arrive shortly
Not ready to buy yet? Download a free sample
We are confident about the unique quality of our Company Profiles. However, we want you to make the most beneficial decision for your business, so we offer a free sample that you can download by submitting the below form
By GlobalDataEvidence of a bounce-back in demand can be found in the latest figures for the UK car finance market.
The consumer new car finance market reported new business was up 37% by value and 32% by volume in November 2021 compared with the same month in 2020, albeit from a low base, according to the Finance & Leasing Association (FLA).
Equally, the consumer used car finance market reported new business was up 55% by value and 33% by volume in November compared with November 2020.
However, cars bought on finance by businesses, over the same period, remained low, with new car demand down 14% but up 4% for used cars.
Peak chip
The auto industry has been one of the hardest-hit sectors by the semiconductor shortages, in large part because the chips it uses represent old transistor technology, which is becoming increasingly less profitable for chip manufacturers to produce.
At the start of the Coronavirus pandemic, auto manufacturers scaled back their production plans at the same time as demand for semiconductors was absorbed by manufacturers of laptops, tablets and other internet-enabled devices, as home working took off.
"Auto manufacturers and auto suppliers took supply chains for granted, so when capacity wasn't booked for a couple of months, semiconductor producers simply moved that capacity elsewhere, where demand from other industries was strong," said Lund of US-based credit rating agency Fitch Ratings.
Once car manufacturers decided on increasing vehicle production, their demand for silicon chips was already out of step with cutting-edge semiconductor production. Silicon chip demand by auto manufacturers remained stuck in 2019 with relatively large chips still being used, while high-end chip production had moved to significantly smaller more profitable wafer technology, increasingly used in the consumer IT sector.
Battery construction costs
Meanwhile, other supply chain disruptions, which may hamper efforts to transition to EV technologies, have become apparent for auto manufacturers.
"The issue for the sector concerns securing what is required for EV production, specifically battery construction and reducing dependence on raw materials," said Lund.
Higher prices for metals such as cobalt, which help stabilise the charging and discharging of EV batteries, threaten to upset automakers' plans for greater electrification.
Approximately 30kg of cobalt is needed for a large battery pack, which at $1,500 to $2,000 represents a substantial cost to the makeup of EVs, which is prompting automakers to consider alternatives to the chemistry for EV batteries, said Lund.
Cobalt on the London Metal Exchange is trading at four-year highs around $70,000 a tonne, the last year alone has seen a substantial increase.
"As BEV programmes proliferate and more low-cost and smaller models are introduced there's scope for introducing more lithium-ion batteries using lower-cost, less-efficient [Lithium Iron Phosphate] LFP-based chemistry that's not reliant on cobalt. As well as being beneficial from a material cost perspective, there's a lot to be said for reducing cobalt reliance from an ESG viewpoint," said MacRae.
More than 70% of the world’s cobalt is produced in the Democratic Republic of the Congo (DRC), and 15% to 30% of the Congolese cobalt is produced by artisanal and small-scale mining, which is associated with human rights abuses, according to a business and human rights expert.
"Child labour, fatal accidents, and violent clashes between artisanal miners and security personnel of large mining firms are recurrent," said professor Dorothée Baumann-Pauly, director of the Geneva Center for Business and Human Rights at Geneva University's School for Economics and Management.
Automotive industry bosses acknowledge "there has to be more investment in the semiconductor supply chain, with many automakers looking to shorten their supply chains and bring key components under their direct control," said Lund.
Pressing issues for automotive supply chains